技术丨基于天然气为燃料的烧成系统的改造与调试
该厂采用的工艺和设备属上世纪80年代初的水平,设备陈旧,工艺落后,能耗高,设备运转率较低,环保不能达标,劳动生产率低,因此水泥厂决定对该生产线烧成系统进行技改。
1、技改方案
1.1 窑尾系统
业主计划对原设计能力为800t/d的烧成系统(实际600t/d)进行技改,最终使系统达到900t/d能力。根据该厂的实际情况,我们新增一台新型离线式管道分解炉:炉体中部设置有缩口、炉体中部和底部之间设有位置可调的燃烧器及炉体底部设置风机等,我们保留了原C2-Ф4200预热器,将原C4预热器改为新系统的C3预热器用,新增一台Ф4 700新型高效低压损旋风筒作为C4预热器,用2-Ф3300新型高效低压损旋风筒取代原有的2-Ф3000作为C1预热器,同时改造进出风管及下料管、锁风阀、撒料盒等备件。通过上述措施,入窑物料分解率达到80%以上,窑的台时产量达到40t/h。
1.2、窑尾废气处理
生产线原配套的增湿塔为Ф5 m;高温风机风量为180000m3/h,全压8000Pa;电收尘器处理风量为180000m3/h;电收尘器后排风机风量183132m3/h,全压2200Pa,排放浓度高达400mg/Nm3。技改方案:采用压缩空气自动喷水系统将常压水雾化,根据烟气温度的变化自动调节喷枪的喷水量,保证烟道出口温度维持在适当的温度范围内;更换了高温风机,处理风量为210000m3/h,全压7500Pa;更换了一台处理风量为210 000 m3/h的三电场电收尘器;更换了一台电收尘器后排风机,处理风量为230000m3/h,全压2200Pa;并改造主要连接风管。上述技改措施使电收尘器出口含尘浓度≤50mg/Nm3,可以满足设计指标和生产要求。
1.3、回转窑及熟料冷却
原有Ф3.4m×77m回转窑切割掉多筒冷却机,改成Ф3.4m×59m,设计更换了传动装置,最高窑速达到3.63r/min。
用篦式冷却机取代原多筒冷却机,并增加窑头罩和三次风管,篦冷机产生的废气采用原窑尾淘汰下来的电收尘器进行处理,可以满足设计指标和生产要求。
2、生产调试
2.1、点火升温
本项目用的燃料是天然气,燃烧器配有电子点火装置,所以相对烧煤来说点火快捷容易。但要保证窑头窑尾处于微负压状态,头排尾排均要开启,否则容易造成天然气燃烧不畅,升温速度不容易控制,导致升温时间过长。
2.2、投料的操作控制
回转窑点火初期,分解炉多次发生塌料以及C2和C3预热器频繁发生堵料,严重时物料多次从分解炉进入三次风管近20m;C3预热器锥体频繁发生堵料,当打空气炮时,料直接冲到窑内,甚至冲到窑前,导致生产几乎无法进行。出现这种现象,我们认为:
(1)操作人员对天然气煅烧操作不熟练;
(2)投炉初期,初始投料量在25~30t/h,高温风机22Hz左右,由于产量低、拉风小导致发生塌料以致堵塞;
(3)没有控制好系统用风以及窑和炉用风平衡,温度倒挂现象较严重,天然气后燃现象较为严重,各级旋风筒温度严重超高而导致堵料;
(4)料入炉的稳定性以及分散性较差,导致窑、炉温度的波动大,窑况不稳定,操作无法稳定。
我们将初始投料控制在45~50t/h,采取大风大料的投料方式,打通系统每级翻板,料从C1预热器顺利入窑,系统温度明显下降,烟室温度相应降低,此时根据系统温度适当减料。预热器系统温度可以短时间适当偏高控制,控制系统温度平衡,目的是降低烧成负荷。根据窑驱动电流的明显变化以及火焰的情况,以及时了解窑的烧成状态是否正常。以上措施使投料初期的不利状况得到了明显改善。
3、调试和生产中的问题处理
3.1、系统堵料和塌料
由于该生产线改为带分解炉的新型干法窑,在生产调试初期,C2和C3预热器常常发生堵料和塌料现象。频繁堵料、系统恶性循环,严重影响窑系统热工制度的稳定和设备安全运转。我们认为主要有以下几点原因:
(1)生料成分波动。有时生料易烧性变得太好,又没有来得及减天然气,生料中易挥发的成分含量增加,引起C2、C3预热器结皮甚至堵塞。
(2)喂料量不均匀。喂料量时多时少,与天然气的给定量不相匹配,将料子烧堵,导致堵塞。
(3)投料初期,由于天然气后燃现象比较严重,温度倒挂,导致相关部位结皮堵塞。
(4)翻板阀动作不灵活,物料下料不均,系统内部短路漏风,引起系统堵塞。
(5)物料中的碱、氯含量过高。在煅烧中这些挥发性组分在窑系统内处于循环状态。它在高温下挥发后到低温区凝结,使物料熔点降低,引起预热器的结皮、堵塞、料流不畅。
针对以上情况,我们主要采取措施严格控制入窑生料成分的波动,根据窑内煅烧情况及时调整生料成分;增加分解炉的分料量,提高入窑分解率,并控制好系统温度和压力。
3.2、回转窑结圈的分析以及预防措施
该生产线烧成系统技改于2010年6月完成并转入负荷试车及试生产,在负荷试车及试生产期间, 由于各方面因素的影响,烧成系统断断续续、开开停停,窑口出现不同程度的结圈现象。
(1)生料成分的影响。由于堆存在库里的粘土结块,高硅粘土和低硅粘土采用抓斗搭配,未经过准确的计量,导致两种粘土搭配计量不准确,混合不均匀;同时由于进磨皮带秤波动较大,致使入窑生料成分波动较大,窑内物料时而难烧,时而易烧,难烧时需慢转窑强烧,易烧时液相量增多,这些都增加了回转窑结圈的可能性。
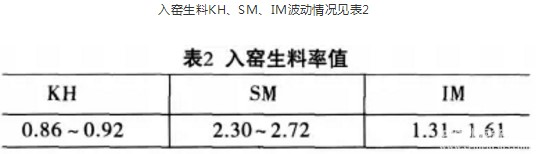
(2)前期调试时,天然气的压力不稳定,天然气给定量不稳定,导致系统温度波动大。
(3)操作不当、热工制度不稳。操作工对看火的基本工作不熟悉,遇到异常情况时,不能冷静分析,盲目急调过度,大起大落,动则大减料、慢转速或急加燃气等,当入窑生料分解率低、预热不好,料难烧时,采取窑头加天然气、烧大火的方法,加之风、天然气、料不匹配,天然气燃烧不充分,用风过大,火焰过长,窑后温度较高,窑速太慢,则易增加窑皮而结圈,同时,三班操作上的不统一,也影响了热工制度的稳定。
我们的经验是:合理选择生料配料方案,生料配料方案选择适宜的KH、 SM和IM;保持入窑生料成分均匀稳定,入窑生料成分应控制在:CaCO3(76.3±0.5)%,合格率大于90%;Fe2O3 2.2%~2.5%,合格率大于90%;同时充分利用现有的均化库,提高生料均化的效果,保持入窑生料成分的均匀性;稳定烧成系统热工制度,不断提高操作水平(稳定烧成系统的热工制度,是防止窑结圈的有效措施之一,在操作上采取“三稳一快”,即“稳定喂料、稳定天然气、稳定窑速、提高快转率”)。
4、正常时系统参数控制
投料量在65~70 t/h,分料量窑炉比为5∶5,三次风阀开度稳定在45%,高温风机转速44 Hz,窑速2.9~3.4 r/min,C1预热器出口氧气含量控制在2.5%~4%。系统参数控制见表3。
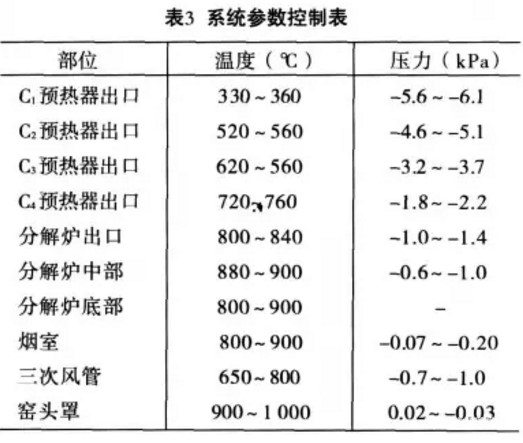
5、配料方案的调整
技改后该厂熟料KH=0.88±0.02,SM=2.4±0.1,IM=1.5±0.1。2010年9月19日入窑生料和熟料分析单见表4。
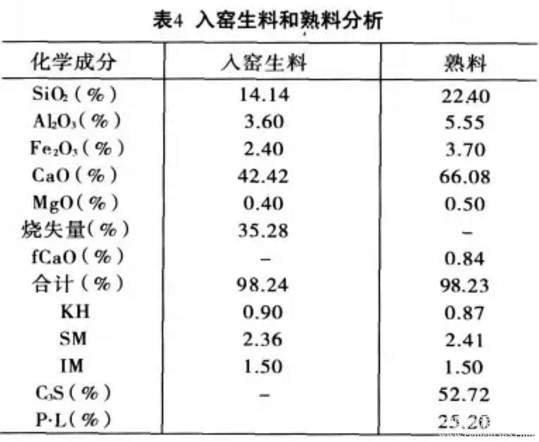
当饱和系数和硅率较合适时,入窑生料CaO含量控制在(42.5±0.25)%范围时,物料易烧性较好,操作容易控制,熟料的fCaO小于1.5%,28d强度基本都在55MPa以上。
6、结束语
(1)由于该生产线采用的设备属上世纪80年代初的水平,原预热器系统比较陈旧,旋风筒的进出风管风速较高,系统阻力大,导致高温风机负荷大,若要继续提高产量和能耗,建议将原有的C2和C3预热器改成新型高效低压损旋风筒。
(2)该生产线在生产过程中,入窑分解率只有80%左右,窑内的热负荷较大,若要继续提高分解率,建议在以后的生产中,在保证上升烟道不至于因温度过高造成结皮的情况下,尽可能减小进入上升烟道的物料,增加入分解炉的物料量,提高入窑分解率;把握好操作控制方法以及优化系统参数,优化配料,防止各种工艺故障,可实现优质高产。
作者:杨顺德 , 田产
出处:中国水泥备件网微信公众号(关注查询更多资讯)
欢迎投稿,投稿邮箱:tougao#cement365.com(#替换为@)
(本文来源网络,若涉及版权问题,请作者来电或来函联系!)