专场丨花3天盲装的减速机,正常运行了17个月
1 前言
我厂拥有一条5 000t/d熟料生产线,2005 年 3 月投产,回转窑配套生料制备系统为从丹麦 F.L.Smidth 公司原装进口的ATOX50辊磨,该辊磨主要参数如下:生产能力:400t/h允许入磨物料最大粒度:175mm允许入磨物料最大水分:8%成品细度:80μm筛筛余≤12%出磨物料水分:<0.5%磨辊个数:3个该辊磨配有瑞士产原装进口马格(Maag)减速机,型号:WPU-200/C- 380,速比 39.76,配套电机功率3 800kW,转速994r/min,其主要结构如图1。
从图1中可见,该减速机系二级减速结构,含一级螺伞,高速小伞齿齿数14,大伞齿齿数50;二级为行星结构,3分支。该减速机特点为高速螺伞悬挂构造,螺伞输出与太阳轮通过花键套(或称为齿形联轴器)连接,传动行星轮,带动磨盘完成动力的传输。在设计产能负荷下,该减速机在重载、振动、粉尘等工作环境中,预期寿命应达15年以上。
2 减速机高速轴失效过程
2012年5月,工厂技术人员发现辊磨主电机与减速机存在相互推挤现象。因无法解释该现象的产生原因,工厂于当年6月初邀请减速机厂家技术专家来工厂进行现场诊断,检查高速轴状况,内容主要有:检查大小伞齿齿面接触情况;检查高速轴轴承润滑情况;检查电机的联轴器橡胶块;检查主电机磁力中心线。
专家得出的结论为:轴承润滑正常;小伞齿面接触略微偏大端(见图2);橡胶块中的 4 块因过载,端面已过热变形;当电机运转时,电机轴会向减速机方向移动5mm,对高速轴施加额外的推力。因此专家建议工厂依据磁力中心线重新找正电机。由于 Maag 减速机检修孔只有 30cm,专家也无法入内触及和贴近察看大小伞齿表面,故同时建议工厂采购大小伞齿及五套轴承作为备件应急。
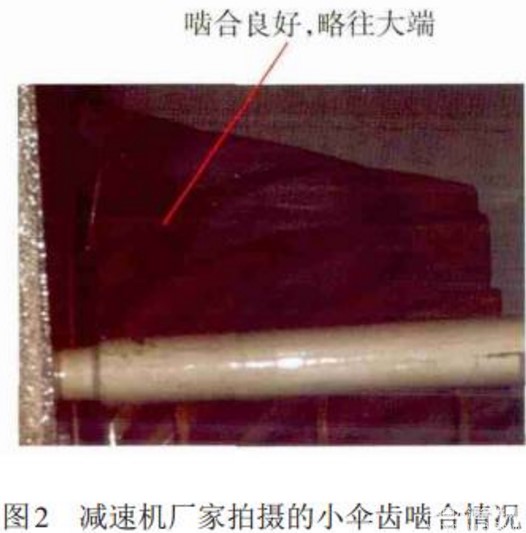
根据 Magg 专家的建议,工厂随后多次对主电机的磁力中心线进行测定,并据此调整了联轴器位置,对联轴器更换了新的橡胶块。但减速机与电机相互推挤的初始状况未有好转。
2012 年末,因辊磨减速机高速轴轴向窜动达120μm,工厂着手准备对减速机进行大修,启动备件的询价采购流程。
2013年3月7日,工厂辊磨正常运转,工况为:投料量510t∕h,主机电流 187.2A(电压 10 000V),研磨压力10.26MPa,料层厚度81.7mm,磨机基础 震动值 1.8mm/s,磨 机 压 差5 230Pa,回料斗式提升机电流32.9A。运行过程中减速机上部旋转部位突然喷出油烟(见图3),并带着较响的气爆声,工厂巡检人员发现情况后立即通知中控停车检查。
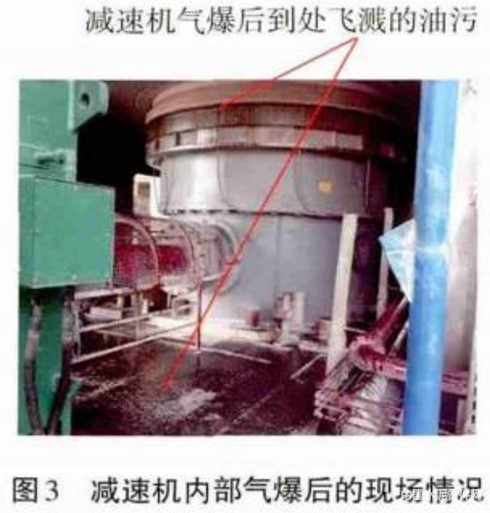
通过打开减速机检修孔初步观察,并核对减速机油站现场触摸屏有无报警点及中控画面有无报警信息,未发现异常状况。需要指出的是,该减速机采购时未订购高速轴测振装置以及相应三套轴承的测温装置,故对有关故障讯息的判断缺少了关键仪表参数支持。因前些年减速机旋转部位也曾发生过疑似甩油现象(较轻),当时工厂技术人员估计是减速机润滑稀油站空气滤芯堵塞引起的喷油,判断无大碍,于是安排恢复开机。
辊磨恢复投料20min后,中控发现主电机前轴瓦温升较快(见图4),现场巡检工也发现电机后端似乎有烟冒出。在双方核实情况的过程中,主电机前轴瓦温度很快上窜到高限报警点,磨机保护启动跳停动作,前后时间不到一分钟。拆开电机前轴承盖检查发现,前轴推力瓦端口已烧毁(见图 5),不能继续使用,需换新瓦。
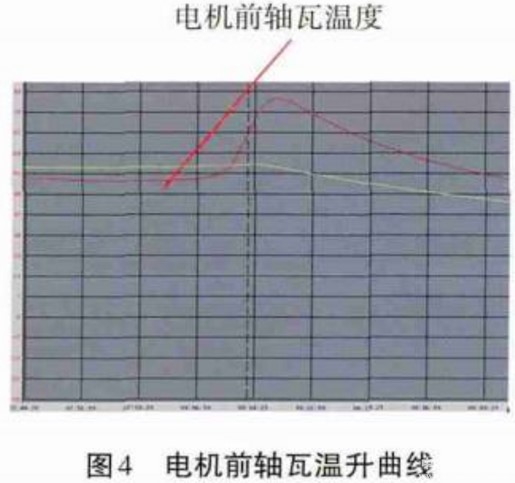
在更换电机轴瓦的同时,工厂维护人员再次打开减速机检修孔进行检查,并拆卸磨机高速轴上端盖,发现高速轴小伞齿头端有明显拉毛痕迹,检测高速轴外端轴承间隙较大,且有明显走外圈现象。电机新轴瓦刮研处理就位后进行空载试车,当机旁开关点动开机后,高速轴端即刻发出明显的异常响声,试车立即停止,根据响声等初步判断,估计辊磨减速机高速轴轴承已损坏,高速轴已失效,无法正常运转。至本次高速轴失效,该辊磨减速机已正常使用8年,共运行35 002h,期间除更换润滑油外,未进行过更换轴承等维修保养。
3 检修方案的选择
由于辊磨高速轴失效突然,工厂一方面马上联系减速机厂家驻国内办事处,要求派员来厂协助检查判断,并提供专业性维护建议;另一方面,回转窑因无生料被迫止火停产,工厂旋即开展对减速机检修方案的筹划。经查发现,辊磨高速轴小伞齿小端已进入啮合,磨损变亮;可见范围内有齿面在中部与尖端已发生较为严重的点蚀;小伞齿前端两个轴承下部、位于减速机底盘上有一堆轴承散架部件(见图 6)。综上情况进一步确认,减速机高速轴前端轴承已损毁。
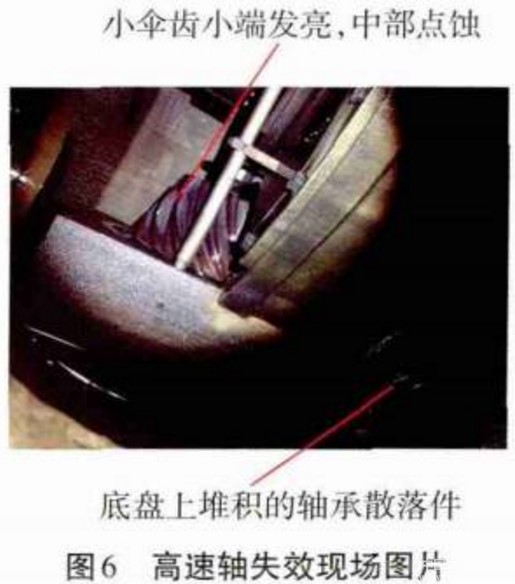
减速机生产厂家分析指出:减速机故障系短时间内对高速轴造成的较大损伤,建议对减速机进行整机拆卸大修,重点更换减速机的高速轴、大伞齿、太阳轮、五套轴承,并检查大伞齿保持架、齿形连轴器、推力瓦支座等。这是一个彻底的维修方案,实施后可对设备长期安全运行提供重要保障。
通过对国内拥有相同设备及有类似故障发生厂家处置经历的了解,鉴于工厂对减速机失效过程发现及时,第一时间停机动作相对到位,加之修复减速机的诸多原产地备件采购存在期限问题,等待国外专家到厂需要时间,如果整机大修预计需耗时15 个工作日以上,且工厂回转窑和水泥生产工艺线处于停机待料状态。经技术部门多方论证,决定对该减速机开展现场临时性维修,重点对高速轴进行现场拆装,更换高速轴的三套轴承,并对减速机内部可察看部分进行检查,以及时恢复生产,减少停产损失。
4 现场维修过程
4.1 高速轴拆卸
人员配备:维修人员5人。主要工具为:气割工具一套,电焊机一套,2t、5t手拉葫芦各2只,扳手等工具一套,撬棒 1 根,ϕ24mm×80mm 螺丝 4只,ϕ24mm × 1 000mm 螺杆 4 根,ϕ24mm×1 000mm丝杆4根。
退出减速机高速轴需用 10#槽钢制作临时口字型工装框架一幅(见图 7),上端比高速轴在现场位置高200mm以上,宽度以高速轴大轴套螺孔对应位置长度为宜。在工装左右槽钢上与高速轴轴套对应螺孔的位置开启用于放置螺杆的圆孔各两个,在卸去大轴套上对应螺栓后,装上螺杆,并在工装上用螺帽固定好。在对应大轴套拆卸孔处旋上丝杆,用于往外顶挤高速轴。在高速轴外端面的四个螺丝孔位置拧上螺栓,用于撬棒的旋转用力支撑点,高速轴外露部分至少用葫芦分段悬挂支撑。
拆卸减速机高速轴时撬棒向正常旋转的方向用力。因该减速机规格较大,伞齿间啮合较紧密,拆卸时施工人员用力需适当,小用力度旋转后,相应拧紧丝杆螺帽配合向外顶挤。拆卸高速轴耗时12h。
4.2 高速轴的维修
高速轴拆出后,发现其前端大轴套处外表面已变成焦黑色,表明此处曾经产生过热,推测内部两只轴承已损坏(见图8),这也正是减速机发生气爆的原因所在。小伞齿有 5 个齿中部或尖端已点蚀。
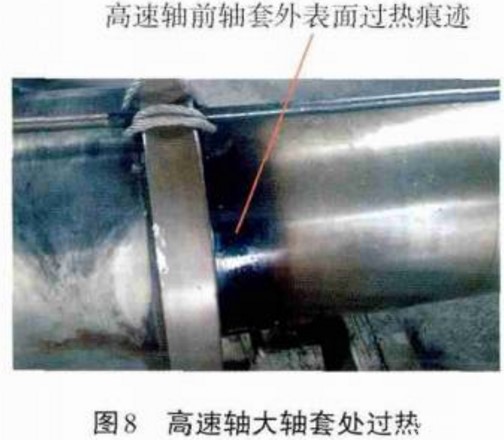
拆下高速轴大轴套发现:高速轴推力轴承档走内圈0.35mm,经研究,对高速轴相关部位进行电镀镀铬加以处理;轴承环走外圈0.50mm,以更换大轴套加以处理;两个轴承的间隔环因磨损进行抛光处理,减少尺寸1mm,为使大小伞齿啮合位置不受影响,相应抛磨减少大轴套与方箱之间的间隔套尺寸1mm;外轴承的小轴套走外圈 0.15mm,同样以电镀镀铬加以处理。高速轴重新组装中使用了三只新轴承,更换前对新轴承进行了测量。组装过程中每装配一个部位前后须测量相关尺寸,并与资料中尺寸要求进行核对,控制在偏差允许范围之内。对小伞齿进行着色探伤,未发现裂纹,对于点蚀部位,用角磨机进行打磨处理。
4.3 方箱裂纹的维修
进入减速机内部检查,发现高速轴支撑方箱轴套孔处有一道 100mm长度的微裂纹(见图9),背面也有一条类似的裂纹,采用气刨、着色探伤与现场焊接处理,背面裂纹焊接好后用钢板加筋强化(见图10)。焊接过程具体注意事项为:
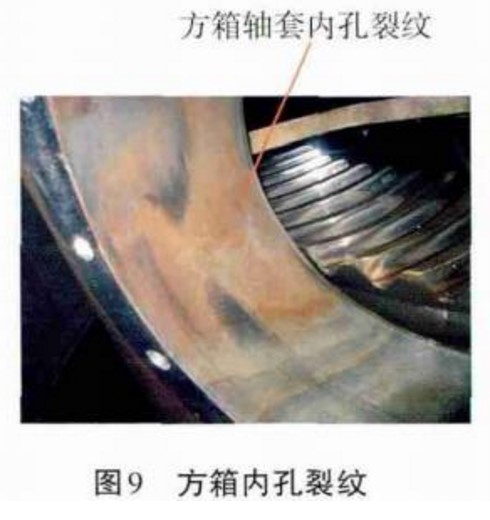
(1)清除裂纹周边表面油污及油漆,确保不会有油流入焊接区域。
(2)用碳弧气刨清除裂纹处金属,并用渗透着色探伤直至无裂纹为止。随后对气刨出的区域用球头铣刀切削掉厚度2~3mm,并仔细清理干净。
(3)对焊接区域用烤枪预热至50℃,加热区域范围尽可能窄。
(4)焊接时环境温度需保持在10℃以上,焊条选用直径 2.5mm、型号为 Ni307、Ni347、Ni307B 焊条。因抢修急需,工厂以Z308作为替代。焊条需经烘箱中250~300℃烘干2h以上,现场使用时用保温筒保温,维持温度100~150℃。
(5)垂直或倾斜型焊缝从底部向上施工。每焊完一遍,仔细清除焊渣,用气动凿子敲击焊缝,消除焊接应力。焊接区域温度不能超过70℃,可在焊缝周围放置浸水的布条或海绵(但不能溢水)用来降温。
(6)方箱轴套内孔焊接全部完成后,仔细打磨焊缝,并随时用内径千分尺校对尺寸。减速机内部其他情况:大伞齿齿形完整,无点蚀等异常现象,中心竖架及联轴器未见异常,减速机内部其他可触及检查的部位无异常。
4.4 高速轴的回装
高速轴的回装按拆卸相反程序进行即可,关键节点是大小伞齿的啮合面检查。可先在小伞齿齿面上涂满朱丹粉,待高速轴就位后通过盘车检查回装质量。由于该减速机检修孔过小,高速轴回装后人员无法进入减速机内部查看啮合情况。解决办法之一是在回装前安排人员待在减速机内部,待高速轴就位,查看完啮合面后,再拆卸出高速轴,人员撤出,重新回装一遍高速轴。解决办法之二是用摄像探头伸入减速机内部,查看啮合状况。前者可仔细分析检修质量,并做出相应调整,但耗时较长,需两次回装高速轴。考虑到工厂抢修时间紧迫,且已严格按减速机生产厂家技术资料的要求组装高速轴部件,工厂采用了摄像探头+电脑显示的办法来检查大小齿啮合面,最终结果判断为啮合尚好,可以达到设备正常运行的标准。
5 后期注意事项
由于事故发生的突然性和应急抢修的仓促性,加上辊磨重载运行的高要求,工厂在减速机恢复投运前制定了新的开机规程,主要有:
(1)辊磨运行参数控制:
辊磨振动值≤1.5mm/s
研磨压力≤9.5MPa
喂料量≤490t/h
其中,振动值为关键控制参数,若振动值超过规定值,要求采取调整喷水量、喂料量、研磨压力、料层厚度、风速等措施。
(2)操作要求:要求中控人员精心操作,时刻关注有关运行参数的变化情况,在第一时间反馈异常信息并可紧急停车。同时,要求操作人员密切关注砂、页岩配料电视监控情况,若有断料发生须提醒配料岗位人员及时处置,防止断料等引起的振动跳停事故。
(3)每天检查高速齿齿面啮合状况,并拍照留档,每周汇总分析。
(4)按照以上研磨参数运行一个月,经检查确认高速齿齿面啮合正常后,研磨压力可加至 10.5MPa,投料量可相应增加,振动值仍按上述要求执行。
6 结语
本次抢修历时 3d。从恢复生产至 2014 年 7 月计划停机更换新的辊磨减速机,以“盲装”形式抢修后的减速机顺利运行了 17 个月,确保了工厂正常生产经营,赢得了采购新备机的宝贵时间。另外,对于同期国内类似引进减速机系统的水泥熟料生产线,由于实际生产工况与设计工况差距较大,普遍加载压力较大,超产较多,给相关减速机内部配件,尤其是高速轴轴承寿命带来较大影响,若在线运行时间已超过 30 000h,建议及时更换维护保养,以防发生突发性故障。
作者:章文明
欢迎投稿,投稿邮箱:tougao#cement365.com(#替换为@)
(本文来源网络,若涉及版权问题,请作者来电或来函联系!)