技术 | 不停窑处理篦冷机高温段故障的实践
2011年1月7日,某公司 5000t/d 生产线在高温段篦床停机 43min,窑系统没有止料停产的情况下,顺利完成了篦冷机高温段液压缸的更换。此次不止料处理故障中,中控操作的重点是不能将一段篦床压死,不能诱发其他事故,尽可能维持窑系统以较高的产量运转。因此中控操作员对篦冷机和窑的承载能力进行了分析,确定了系统的减料幅度并提出操作方案。
1 事情经过
1月7日15:30,篦冷机巡检工在接班时发现篦冷机高温段北侧液压缸漏油严重,影响其正常运行,要求中控止料更换液压缸。 根据以前的经验,更换液压缸需要 50~100min。按照公司《中控窑操作业指导书》的 规 定,高温段篦床停机超过 10min,窑必须止料。 但考虑到系统检修后刚刚转入正常,为了避免因止料造成的温度突变,使刚更换的篦冷机顶部和窑头罩前墙浇注料受损,决定不止料停产更换液压缸。调度通知各相关人员于 16:30 停篦冷机,留 1h 时间便于在篦冷机停机之前充分做好各方面的准备工作,如准备现场工具、备品、备件,熟练操作人员到岗以及对系统参数做出调整。 要求把更换液压缸的时间压缩在 40min 以内,且保证窑系统在此期间不能止料。
2 中控处理措施
2.1 以前处理方法
以前曾尝试过不止料处理高温段篦床故障,但均没有取得成功,同时还诱发了其他工艺事故,延长了处理时间(见表 1)。因此 2009 年 9 月以后,遇到此类故障都是严格按照规定,采取止料停窑的保守操作。
2.2 篦冷机和窑的承载分析
2.2.1 篦冷机承载分析
篦冷机型号为 LBTF5000,有效面积为 121.48m2 ,篦床是复合篦床,分为三段,每段又分三个室。一段篦板分布情况见表2。
该段一室有 6 排固定阶梯篦板,二室有 5 排固定充气篦板,在一室和二室交接处有一个500mm 的垂直台阶。这种设计有以下优点:
1、从固定阶梯篦板的篦缝吹出的水平喷射气流,把流态化细粉吹送到熟料层表面, 在脉冲气流作用下,细粉熟料既不会循环在篦板上喷砂,也不会滞留在粗料空隙中影响气流流动,所获得的熟料层分布均匀而透气。
2、一室和二室都只有 3 排活动篦板,由于活动部件少,设备运转率高,承载能力较强,正常生产时,一段篦床上料层厚度控制在800~850mm,根据操作经验,一段篦床停机时,一室料层厚度控制在 2m 以下,重新开机后不会发生压床事故。一室的有效面积为 15m2,如果料层厚度按照2m 控制 ,熟料量约为 43.5t。
3、一段篦床停机后,一室篦床上的物料堆积到一定高度后,部分熟料在自重和空气炮作用下向二室移动,一室和二室之间的垂直台阶为容纳较多物料提供了条件。
因此当一段篦床停机后,将出窑熟料量控制在50t 以下,可以保证一段篦床不被压死。
2.2.2 窑承载分析
回转窑规格为 Φ4.8m×72m,要想保证篦冷机不被压死,40min 内出窑物料量应控制在 50t 以下。接班时窑转速为 3.9r/min,投料量为 370t/h。 根据下面的三个公式,设料耗为 1.6kg/kg,计算得出窑内物料负荷率为 7.33%,物料在窑内的停留时间为 22min。窑速维持不变,将投料量降为 200t/h,则 22min 后窑内负荷率将降低到 3.96%。篦冷机停机后,窑速按照 2.0r/min控制,3.96%的负荷率相当于 102t/h 的投料量,40min内出窑熟料在 42.5t,在上述分析的篦冷机承载范围以内。
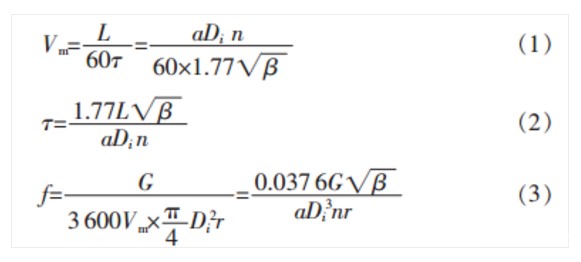
为保证故障排除后,系统能够尽快恢复正常煅烧,在一段篦床停机后,将投料量增加到 250t/h,窑速维持2.0r/min 不变,窑内负荷率将逐渐增加到 9.66%,窑尾不会发生漏料现象。
2.3 系统参数调整
中控根据上述分析将操作过程细化分解为 3 个阶段。 停机前降低窑内物料的填充率,降低一段篦床上的料层厚度,控制在 100~150mm;停机后加强窑内的煅烧控制,防止塌料、跑生料事故;开机后防止一段物料涌入二段将二段压死,同时要避免结块料将破碎机卡死。 据此,中控于 15:50 开始对系统参数作出相应调整,见表3。
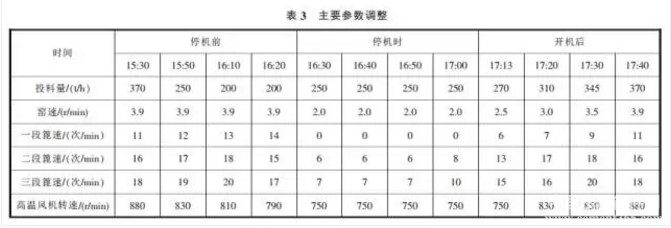
3 效果
17:13 换好液压缸, 比预定时间推迟了 3min,但此时通过篦下压力和篦冷机监控电视画面观察,篦床上还有继续入料的余地,也就是说,在维持一段篦床停机时的窑速和投料量下,篦床还能推迟开机,或者投料量和窑速还有提高的空间。 17:40 系统投料量和窑速恢复正常,篦冷机运行正常。
4 操作注意事项
4.1 窑内物料量和窑速的控制
在篦床停机前, 应适当降低窑内物料填充率,便于在篦床停机后入一段的物料量控制在 50t 以下。 操作员可根据当时的窑速、窑皮的厚薄、有无结圈等综合判断物料在窑内的停留时间,然后按照停机所需时间的长短确定减料的幅度。待减产后的第一股物料进入篦冷机后再降窑速,停篦床,此时窑内物料要在不压窑、窑尾不溢料的前提下尽量保持较高的填充率。
4.2 熟料结粒的控制
操作上应加强窑内煅烧温度的控制,勤观察窑主电动机电流和窑头看火、 篦冷机料层厚度监控电视,关注窑内火焰温度和物料带料高度、熟料结粒、翻滚情况以及离窑熟料温度,发现变化及时调整,调整幅度尽可能小,尽量使熟料结粒细小均齐。必要时,中控操作员应到现场看火,观察窑内煅烧状况。
4.3 篦冷机的操作控制
4.3.1 篦速、料层厚度的控制
停机前,一室篦床上的料层厚度尽可能控 制在 100~150mm,应密切关注一段篦下各室的压力和驱动电动机电流的变化情况,及时调整篦速。由表 1 可以看出,处理这类故障时,二段篦床压死的几率比一段还高,除了篦床本身结构的影响外,很大程度上都是由于一段篦床开启后,篦速提高过快造成物料大量涌入二段所致。因此一段篦床开启后,应在最低篦速上运行几分钟, 这时如果二段篦床的驱动电流、 油压或篦下压力中有任一参数发生剧烈变化,应立即停止一段篦床的运行,确保二段的安全。
一段篦床停机前,二、三段篦速的控制要尽可能延长物料在篦床上的停留时间,弥补因减料慢窑后出料减少造成的二、三次风温下降对窑内煅烧的不利影响。开机前 10min 应加快篦速,把二、三段篦床上的料层厚度控制在最低,以迎接一段篦床开机后大量物料的到来,并尽快恢复正常控制。
4.3.2 篦冷机冷却风量的控制
料层厚时增加冷却风量,料层薄时减少冷却风量。防止发生冷却风短路,或因冷却风量不足使物料黏结。具体的调整可参考表 4。
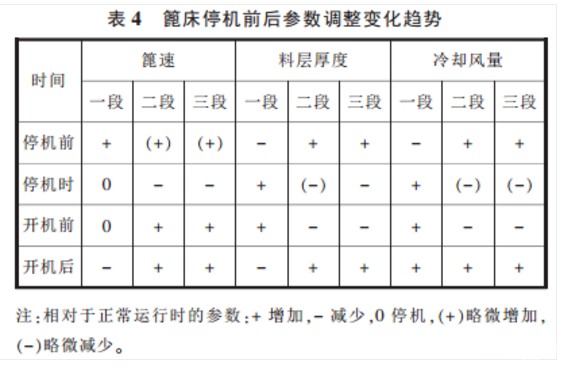
4.3.3 篦冷机空气炮和破碎机的控制
在一室料层达到 400mm 时开启篦冷机空气炮自动循环,达 到 600mm 时将循环间隔时间调整到 5min,1 000mm 时转换到手动控制,不定时的开启,使一室堆积的物料尽可能的向下游篦床移动。一段篦床上的物料有时会黏结成块。但这种块状物料大多成葡萄串状、易碎,在篦床的往复运动中往往能自行裂开,进入破碎机时不会对其构成威胁。中控操作员应通知现场巡检工观察三段篦床上的料层厚度、结块料的大小、数量及位置,并及时反馈给中控。 如果结块料太多或者后续物料量太大,中控应根据破碎机电流的变化间断开停三段篦床,确保破碎机的正常运行。
4.4 预热器系统的控制
减料时,系统风量应同步降低,该公司低产量运行时 C2A 和 C4B 容易发生堵塞, 故在减料前安排专人定时活动翻板阀,帮助排料。同时将预热器系统的空气炮和环形吹堵的循环间隔时间由原来的 30min 调整为 5min,避免物料在锥部堆积。
5 结束语
对于不同的生产线,窑况都不一样,所以,应结合各厂的具体情况加以修正,避免不必要的停机,保持系统热工制度的稳定。在处理这类故障时,一定要结合篦床本身的结构,确定合理的承载能力,既要避免估算过低,造成不必要的停机,又要避免估算过高造成压床事故,同时在故障处理结束后篦床开机前卸荷油压应尽可能调高,篦床正常运行后,再将其恢复到正常油压范围。
来源:《水泥》
中国水泥备件网微信公众号(关注查询更多资讯)
(本文来源网络,若涉及版权问题,请作者来电或来函联系!)